Context
A food industry manufacturer needed to renew an ageing double big bag filling station for processing powdered milk.
A closer look at the installation
Iserco designed, manufactured and installed a set of two semi-automatic big bag filling stations with a framework and access footbridge between the stations. The entire equipment is made entirely of stainless steel.
The challenges
The design office encountered 3 main challenges in the design of this project.
The first obstacle was the space available on site to integrate the entire installation. A 3D scan was carried out at the client’s premises to enable the design office to draw up its plans with the utmost precision and thus ensure perfect integration of the filling stations. The entire installation is completely custom-made.
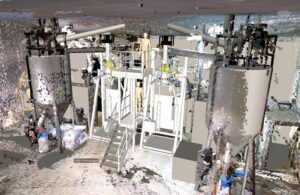
Integration of big bag filling stations into the 3D scan
The second challenge concerned the product to be conditioned. Powdered milk is fairly dry, but it is sensitive to moisture and can become sticky. As a result, during filling, slopes are formed and the filling of the big bag is not optimal. The bag must be extended to avoid any risk of blockage.
The third challenge was linked to the hygiene standards imposed by the food industry. The system is designed and manufactured to allow disinfection, complete cleaning and to prevent contamination of food products. This is guaranteed by an EC declaration of conformity to hygiene and occupational safety regulations.
The proposed solution
The customer needed a double big bag filling station in stainless steel.
The powdered milk to be conditioned is stored in two silos. It is transferred to the filling stations by means of Archimedean screws. Before filling the big bag, the product passes through a 2-way distributor. The product is directed to the filling chute or to a waste outlet if it is contaminated. Product contamination is detected by a device placed at each filling station. It can reveal the presence of ferrous substances (magnetic or not) in powdered milk.
The installation is also equipped with a mobile stainless steel apron allowing the big bag to be extended during the filling phase. The powdered milk has a large angle of repose due to the screw feeder. The operator mounts the mobile apron and then starts the cycle via an HMI. As the filling process progresses, the apron is lowered to allow the big bag to rest on its pallet.
The big bag lugs are held in place by automatic hooks, equipped with a system of cylinders that open at the end of the filling process.
The installation is equipped with a Clean Connect, which allows total containment of the big bag by clamping the bag. This system avoids contamination of the big bag, both inside and outside.
This system is made of a double skin with a suction nozzle and a nozzle for pre-forming the big bag. Each spigot is equipped with a butterfly valve to optimize the filling and the air extraction phase (of the particles).
In order to avoid folds on the big bag fabric and to ensure the correct filling, our stations are equipped with a blower. Siad blower is equipped with a filter box which allows the air blown into the empty big bag to be purified, thus avoiding the risk of contamination.
The filling stations are also equipped with a densification table which ensures the deaeration and compaction of the product by vibration. This ensures optimal filling of the big bag and retention on the pallet.
The machines are supplied with an electrical cabinet which ensures the complete control of the big bag filling stations. The control panel is equipped with weighing software that allows the weight and commercial dosage of the product. A filling is controlled by a PLC, which stops the machine when the weight is reached. These filling stations can handle several sizes of big bags, so the customer can modify the recipe according to the big bag chosen for the conditioning.
The assembly and commissioning are carried out by the ISERCO team. The operators were also trained and tests were carried out at the customer’s premises.
Bulk information
- Type of industry: Food / Agri-food
- Product : Powdered milk
- Conditioning : big bag
- Product density : 0,4
- Particle size: about 5 µm